Temperature Estimation of Vital Components in Electric Motors Using Machine Learning
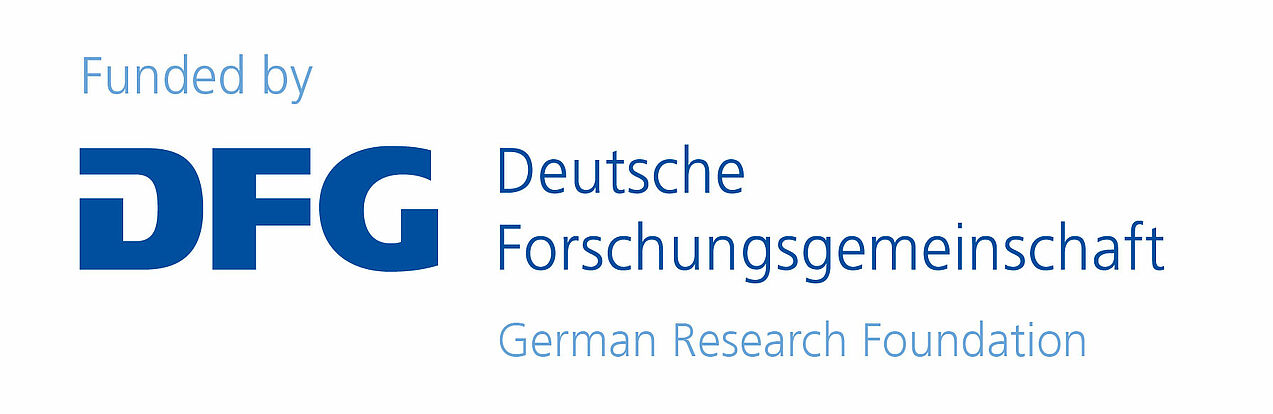
Project acronym: DFG-ANN
Project period: 3 years (2018/07/01 – 2021/06/30)
Project partner: German Research Foundation (DFG) under the reference number BO 2535/15-1
Motivation
In order to exploit an electric motor's full capabilities, high thermal stress on the motor's potentially failing components must be taken into account, that are the stator winding insulation, which may melt, and the permanent magnets that can suffer from irreversible demagnetization.
A sensor-based temperature measurement would yield a rather precise thermal state knowledge, yet for the rotor part, it is technically and economically infeasible due to an electric motor's sophisticated internal structure and the rotor's difficult accessibility.
Stator temperature monitoring is realized with thermal sensors, but these are usually firmly embedded in the stator precluding any replacement, although sensor functionality deteriorates steadily.
Since competitive pressure demands perpetual reduction of production costs, there is a commercial interest driving the investigation of sufficiently accurate real-time temperature estimation.
In the last decades, various research efforts led to approaches that approximate the heat transfer process e.g. with equivalent circuit diagrams called lumped-parameter thermal networks (LPTNs).
This kind of model must forfeit physical interpretability of its structure and parameter values by significantly curtailing degrees of freedom in favor of the real-time requirement and, at the same time, expert domain knowledge is mandatory for the correct choice of parameter values.
In contrast, neural networks are known to be universal generalizers, with gradual degrees of complexity that can be adapted to the capacities of the application platform.
A unifying algorithm that adapts on various electric motors, their geometry-varying components, and application-specific dynamics solely through recordings is expected to supersede classical approaches, that yet dominate the field of temperature modeling.
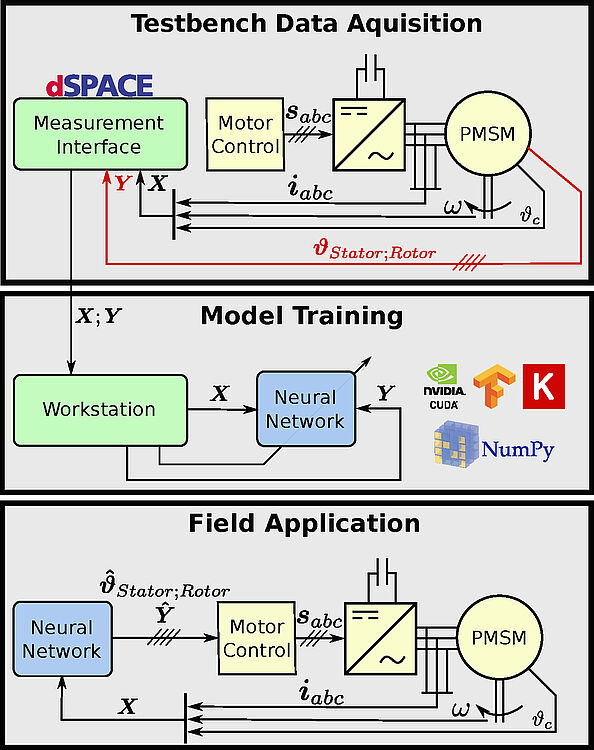
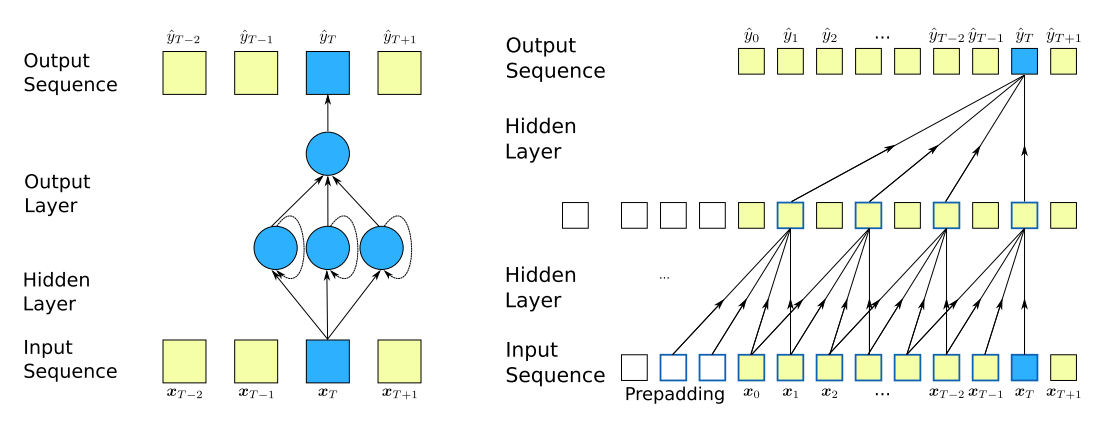
Project goals
The goal is to parameterize neural networks entirely on empirical data, exploiting their rich expressive power without the need of motor sheet data.
Having test bench data available, estimation accuracy on real-world data is precisely reportable, and has been investigated for the first time in literature by [1].
The entire process from data acquisition over model training up to temperature monitoring in the field is sketched in Fig. 1.
More specifically, in the field of sequence learning tasks, recurrent neural networks (RNNs) and convolutional neural networks (CNNs) denote the state of the art in classification and estimation performance.
Their topology is depicted in Fig. 2.
They were studied in [2] and showed superior performance in terms of common regression metrics.
However, they exhibit hundreds of thousands of trainable parameters, which render a lean application on best-cost embedded hardware infeasible so far.
Across the domain of supervised machine learning, linear regression has also been shown to perform competitively [3] with the advantage of running on very few parameters, albeit not as few as classical physics-based models.
Apart from linear regression and neural networks, data-driven supervised learning algorithms, that stem from the computer science field of pattern recognition from the last decades, were displayed to not achieve sufficient estimation accuracy [4].
Another shortcoming of the so far investigated approaches is the dependency on exponentially weighted moving averages and standard deviations of definite filter strengths, that are expected to be suboptimal in some operation points.
The project is expected to be concluded with an innovative neural-network-based architecture, that incorporates domain knowledge and combines the benefits of both worlds, data-driven black box models from the machine learning regime and thermodynamic white- or grey-box models, such that a steady estimation on an embedded traction drive control system is feasible in real-time.
References
[1] | O. Wallscheid, W. Kirchgässner, J. Böcker "Investigation of Long Short-Term Memory Networks to Temperature Prediction for Permanent Magnet Synchronous Motors" International Joint Conference on Neural Networks (IJCNN), IEEE, pp. 1940-1947, Anchorage, Alaska (USA), 2017 |
[2] | W. Kirchgässner, O. Wallscheid, J. Böcker "Deep Residual Convolutional and Recurrent Neural Networks for Temperature Estimation in Permanent Magnet Synchronous Motors" IEEE International Electric Machines Drives Conference (IEMDC), pp. 1439-1446, San Diego, CA (USA), 2019 |
[3] | W. Kirchgässner, O. Wallscheid, J. Böcker "Empirical Evaluation of Exponentially Weighted Moving Averages for Simple Linear Thermal Modeling of Permanent Magnet Synchronous Machines", Proceedings of the 28th International Symposium on Industrial Electronics (ISIE), pp. 318-323, Vancouver, BC (Canada), 2019 |
[4] | W. Kirchgässner, O. Wallscheid, J. Böcker "Data-Driven Permanent Magnet Temperature Estimation in Synchronous Motors with Supervised Machine Learning" ArXiv-Preprint, arXiv:2001.06246, 2020 |
Contact:
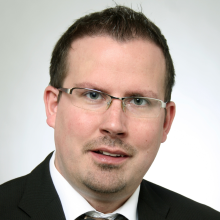
> Leistungselektronik und Elektrische Antriebstechnik (LEA)
Leiter - Vertretungsprofessor - Vertretungsprofessor Leistungselektronik und Elektrische Antriebstechnik
Büro: E4.310
Telefon: +49 5251 60-3881
E-Mail: schafmeister@lea.uni-paderborn.de
Web: Homepage