Development environment and demonstrators for resonant power conversion facilitating high voltage test systems using very low frequency and DC-sources

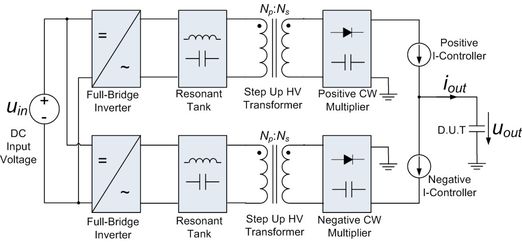


Nowadays, application-specific development environments play an increasingly important role for power electronic designers. They aim to reduce costs, time to market and required design expertise and to increase market share by setting up a development environment, assisting the designer and allows building of resonant operated power supplies. In the project RPC-HVTS-DCS such an environment is developed for very low frequency (VLF) true sinus high-voltage test systems (HVTS) (Fig. 1 and Fig. 2) [1-5] and DC-sources (DCS) (Fig. 3) [6] [7]. The following models are developed an integrated in the development environment:
- A computer aided DC and AC analysis (CAA) of resonant operated power electronic circuitry based on a computer algebra system.
- Design of power electronic and control circuitry based on high-voltage (HV) cascade, current-controller (I-controller) models and generalized averaging techniques. It is supported by (a).
- Design of magnetic components, taking care of intra/inter winding and stray capacitances of high voltage windings and high-frequency effects.
- Thermal design using approximate thermal modelling of power semiconductors and magnetic components.
- The availability of novel macro models for power electronic circuits and characteristics for loaded HV-cascades (b) supporting small and large signal modelling should enable total VLF-generator simulation e.g. for control design, models for magnetic components with respect to electrical (c) and thermal behaviour (d) upgrades PLECS and simulation results.
- Computer aided optimisation (CAO) of the power circuitry and magnetic components with respect to selected cost functions which might be efficiency, weight, current and voltage stress of components by applying modern numerical optimisation algorithms.
With in the research project the development environment is directly applied to optimize the classical unidirectional HVTS, to design a novel bidirectional HVTS and to develop the next generation DCS with higher dynamics (Fig. 4 and Fig. 5). By building these three demonstrators the development environment shall be validated.
References:
[1] | M. Hu, N. Fröhleke and J. Böcker Frequency / Duty Cycle Control of LCC Resonant Converter Supplying High Voltage Very Low Frequency Test Systems 13th European Conference on Power Electronics and Applications (EPE2009), Barcelona, Spain, 2009 |
[2] | Z. Cao, N. Fröhleke and J. Böcker Control Design for a Very Low-Frequency High-Voltage Test System 13th European Conference on Power Electronics and Applications (EPE2009), Barcelona, Spain, 2009 |
[3] | M. Hu, N. Fröhleke and J. Böcker Small-Signal Model and Control Design of LCC Resonant Converter with a Capacitive Load Applied in Very Low Frequency High Voltage Test System IEEE Energy Conversion Congress and Expo (ECCE), San Jose, USA, 2009 |
[4] | Z. Cao, N. Fröhleke and J. Böcker Converter and Control Design for Very Low-Frequency High-Voltage Test Systems IEEE Energy Conversion Congress and Expo (ECCE), San Jose, USA, 2009 |
[5] | Z, Cao, M. Hu, N. Fröhleke and J. Böcker Modeling and Control Design for a Very Low-Frequency High-Voltage Test System IEEE TRANSACTIONS ON POWER ELECTRONICS 25(2), 1068-1077., 2010 |
[6] | J. Lv, Z. Cao, N. Fröhleke, J. Böcker and H. Yuan Thermal-Electrical Simulation of Resonant Operated DC-DC Converter Based on Extended Describing Function Method 14th European Conference on Power Electronics and Applications (EPE2011), Birmingham, UK, 2011 |
[7] | Z. Cao, F. H. Nzeugang, N. Fröhleke and J. Böcker A comparative study of series-parallel resonant converter by using different modulation strategies 37th Annual Conference of the IEEE Industrial Electronics Society (IECON2011), Melbourne, Australia, 2011 |