Increase of Functional Safety and Fault Tolerance of Electrical Drive Systems
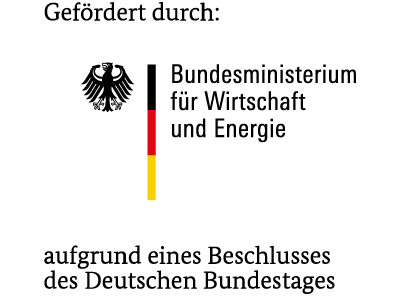
The research project is funded and supported by the Federal Ministry of Economics and Energy (BMWi) within the framework of the research initiative 'ATEM – Drive Technologies for Electric Mobility'
Project acronym: SichElAn
Funding period: 3 years
Project partner: ZF Friedrichshafen AG
Project manager: http://pt-em.de
In this research project the work group LEA collaborates with the industrial partner ZF with its company headquarters in Friedrichshafen, Germany. ZF is a global leader in driveline and chassis technology as well as active and passive safety technology.
Motivation
With the use of electrical drive systems in traction applications and the related high requirements on reliability, safety and functional guarantee the importance of condition monitoring, fault diagnosis and fault isolation aspects is growing continuously. The system architecture of electrical vehicles is very complex and it will become even more complex with the increasing level of developments in the future. The ongoing increase of complexity will lead to an indispensable higher probability of technical malfunctions within the overall system. This leads to great challenges for safety related system functions concerning fault detection and isolation (FDI) as well as short failure response times to ensure a high level of system reliability and robustness regarding the analysis of the current process state. The core challenge is not only a reliable detection and isolation of malfunctions or rather failures within the system but especially the initialisation of a smooth automatic transfer, with short delay times, from undesirable to secure process states according to functional safety rules. The overall goal is to minimize the risk potential for damages or serious accidents and if applicable to maintain the system operation even with reduced system performance.
The continuous developments of modern computing platforms (short computational dead times, parallel computing of independent program sections, etc.) allows a cost-effective extension of technical systems to improve the failure safety, function safety and operational safety through software-based redundancy within the considered system. Thus, the basis for introduction of model-based techniques and methods is given. However, for the electrical drive system there is so far no uniform concept realizing safety relevant monitoring, failure diagnosis and failure management functions which fulfils all criterions of international standards for safety relevant aspects of electrical systems (e.g. the functional safety standard ISO 26262, titled "Road vehicles – Functional safety").
Project goals
Fail-safe and if applicable fault-tolerance operation of the electrical drive system
- Primary goal (fail-safe):
- Increase of the system safety with respect to random appearing, unpredictable failure occurrences within the electrical drive system
- Secondary goal (fault-tolerance):
- Increase of the system availability (maintenance of system operation even with reduced system performance despite of failure occurrences within the system)
- The goal can only be fulfilled if there is no conflict with the primary goal
- Gain of deep knowledge in the research field of functional safety

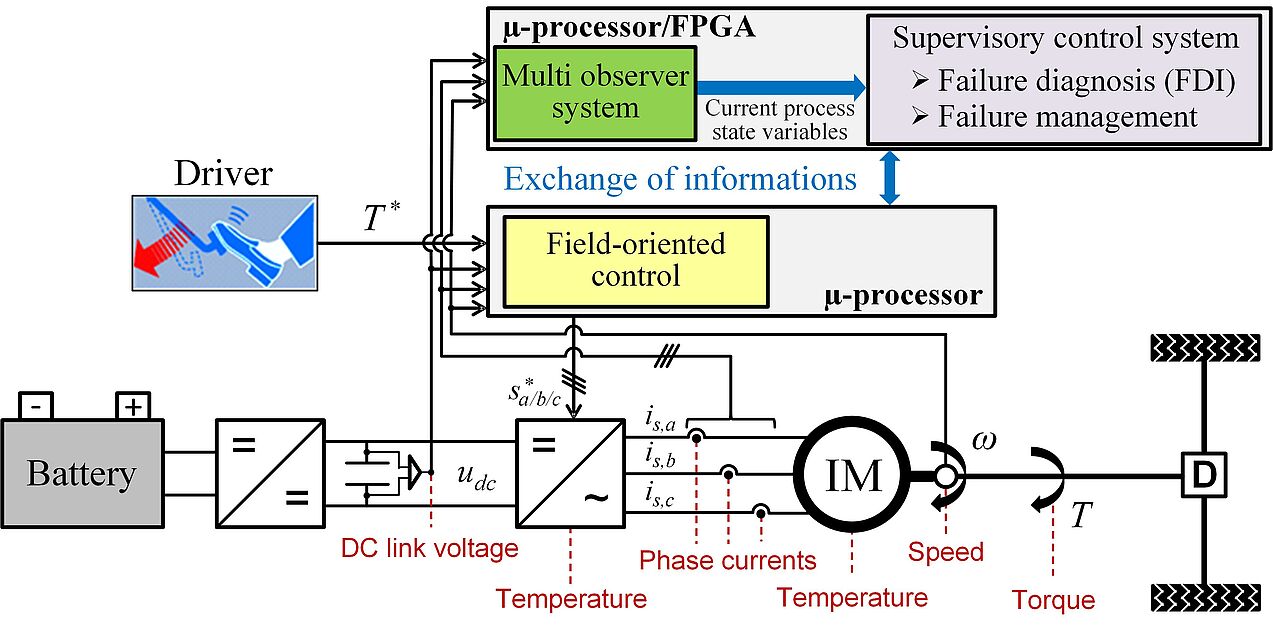
Solution-oriented approach
Within the project a solution-oriented approach will be investigated which essentially consists on the utilization of known model-based techniques and methods for condition monitoring, failure diagnosis and fault-tolerant control of electrical drives. Therefore, for the chosen electrical traction drive system especially the specific characteristics of the electrical machine (e.g. non-linear magnetisation behaviour, high power density or rather highly integrated drive structure, temperature dependency, etc.) and the inverter (non-linear characteristics, temperature dependency, etc.) have to be considered within the modelling process. As a result of the investigations a uniform concept for a supervisory monitoring and management control level shall be developed, validated on the test bench and critically evaluated regarding the requirements specified in advance. Therefore, during the ongoing operation the current process state must be determined, failure diagnosis functions must be executed and appropriate measures, in case of a detected malfunction within the system, must be self-acting initiated. Suitable reactions could be e.g. the switchover from a faulty sensor signal to an equivalent observer signal, if need the reconfiguration of the control approach, etc.
In Fig. 1 the current state-of-the-art for configuration of an induction motor drive system is illustrated and Fig. 2 shows the target structure which shall be realized within the project period.
Responsibilities of LEA within the project
The work group LEA is responsible for the following tasks:
- Analysis of the overall system with methods of the probabilistic safety analysis (PSA)
- Design of a uniform condition monitoring, failure diagnosis and management concepts
- Development of the software modules
- Verification of the developed methods