Multi-Motor Drive System (MMDS)
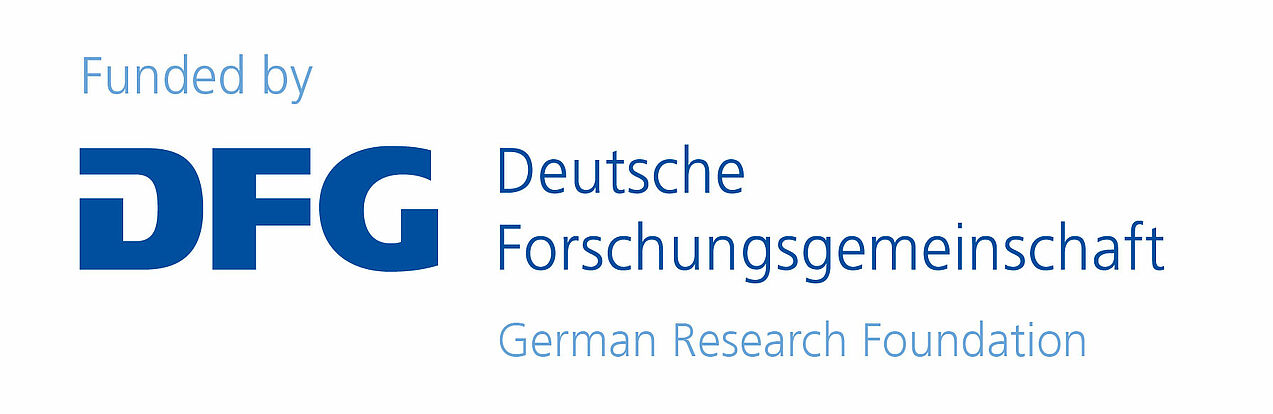
Project acronym: DFG-MMDS
Project period: 3 years (2018-2021).
Project partner: German Research Foundation (DFG) https://gepris.dfg.de/gepris/projekt/389029890
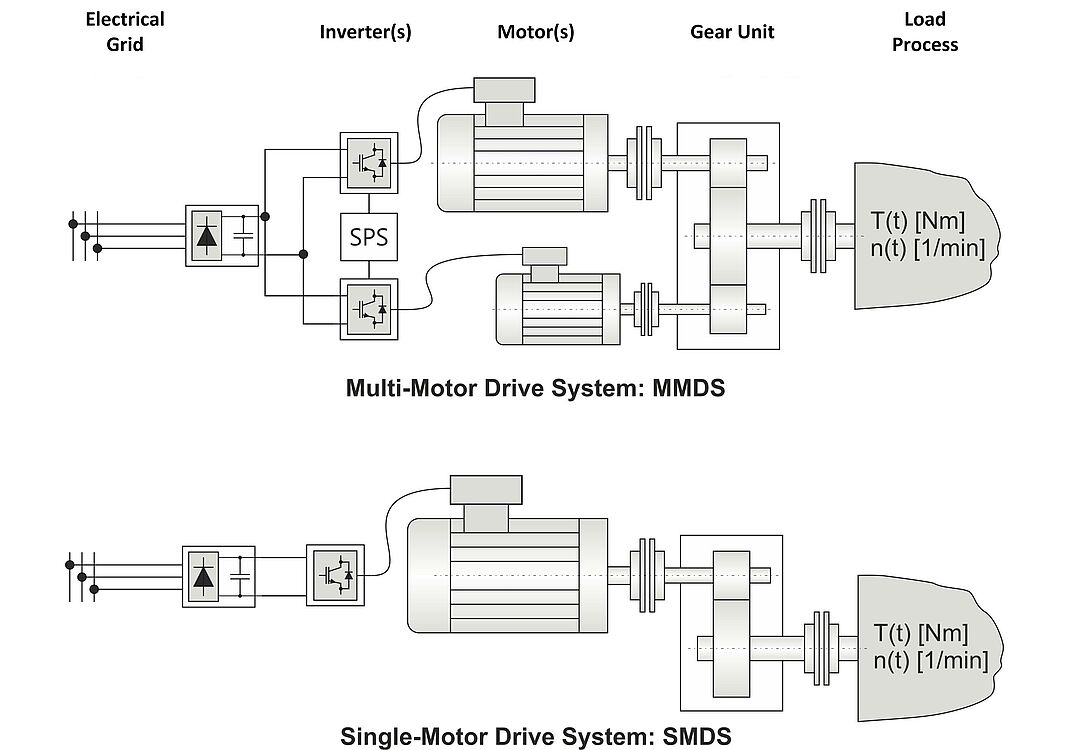
Motivation
One approach to increase the energy efficiency of drives is the use of a multi-motor drive system (MMDS), which consists of a drive system of two or more motors and, depending on the application, a gear unit, which together solve the drive task (compare Figure 1). MMDS are an attractive alternative to conventional drives consisting of one motor (SMDS) due to the following advantages:
- Higher partial load efficiency,
- Increased system availability through modular fail-operational capabilities, and
- Increased degrees of freedom in system design.
In the industry, MMDS are currently only found in niche applications, whereby the rubber mixing process in the automotive supply industry is to be mentioned here as a representative example. Due to the trend towards detailed adaptation of the automation components to the requirements of the production system, increased attention to this concept is expected in the coming years. From a scientific point of view, MMDS are almost completely unexplored in terms of system modelling, operation strategy and design. Especially the influences of an MMDS concept on power electronic components have not been considered yet. In order to apply MMDS in a wide range of areas, a generalized system consideration detached from the individual industrial application as well as an extension of the horizon of consideration to the entire drive system from the supplying network to the load process is necessary. This approach should lead to general design methods for MMDS. Thereby, a catalogue of procedures and algorithms shall be developed, which enable a highly automated design process of a MMDS. By combining the mechanical and electrical analysis of the MMDS drive system, a holistic system understanding is reached which takes also the interactions between both domains into account. This project is a cooperation project of LEA and the mechanical engineering department KAt (Prof. Zimmer) of Paderborn University
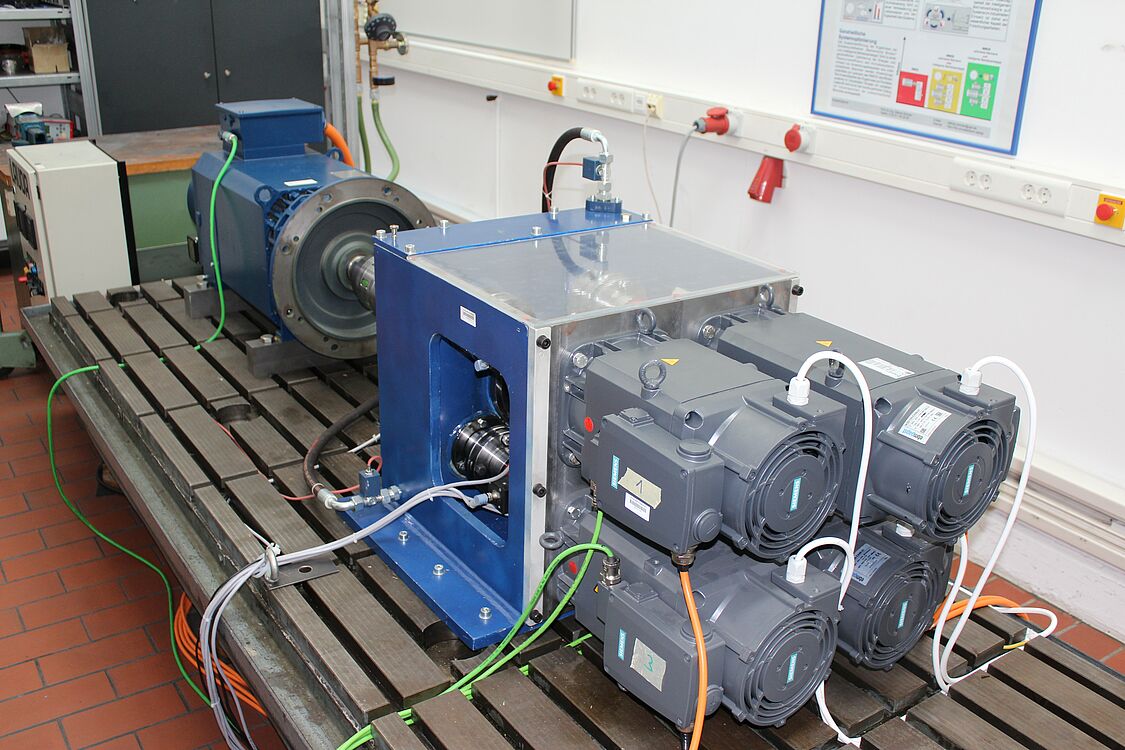
Project goals
An in-depth investigation of MMDS in the aspects of holistic modelling, operation strategy and design is necessary to enable a systematic and meaningful comparison between MMDS and SMDS. In addition, the risk of a sub-optimal design of an MMDS system regarding the resources, which are needed to set up and operate the MMDS, is reduced. With the help of this project, a significant contribution to resource efficiency for MMDS applications is focused.
The key project objectives can be summed up as:
- Holistic modelling: electrical-mechanical modelling of MMDS
- Holistic controller synthesis: Active elimination of vibrations within the mechanical connecting elements by means of precise torque estimation and control
- Optimal system design: Creation of a procedure for the selection of the optimal MMDS topology
From the electrical engineering point of view, the following investigations are of particular importance:
- Modelling of inverter behavior, flux and torque estimation for asynchronous motors, thermal behavior, losses, ageing effects,
- Efficient operation point control and high dynamic torque control, and
- Operation strategy of the MMDS using self-optimizing approaches.
References
[1] | U. Brückner, M. Strop und D. Zimmer |
[2] | M. Strop und D. Zimmer |
[3] | O. Wallscheid, M. Meyer und J. Böcker |
[4] | M. Stender, O. Wallscheid und J. Böcker |
[5] | M. Stender, O. Wallscheid and J. Böcker "Accurate Torque Estimation for Induction Motors by Utilizing Globally Optimized Flux Observers," 2020 International Symposium on Power Electronics, Electrical Drives, Automation and Motion (SPEEDAM), Sorrento, Italy, 2020. |
[6] | M. Stender, O. Wallscheid and J. Böcker "Comparison of Gray-Box and Black-Box Two-Level Three-Phase Inverter Models for Electrical Drives," IEEE Transactions on Industrial Electronics, Volume: 68, Issue:9, Sept. 2021 |
[7] | M. Stender, O. Wallscheid and J. Böcker "Accurate Torque Estimation for Induction Motors by Utilizing a Hybrid Machine Learning Approach,” 2020 IEEE 19th International Power Electronics and Motion Control Conference (PEMC), Gliwice, Poland, 2020 (postponed to 2021). |
[8] | M. Stender, O. Wallscheid and J. Böcker "Gray-Box Loss Model for Induction Motor Drives,” 2020 IEEE 19th International Power Electronics and Motion Control Conference (PEMC), Gliwice, Poland, 2020 (postponed to 2021). |
[9] | M. Stender, O. Wallscheid and J. Böcker |